Dichtheitsprüfaufgaben bei Elektronik und Sensoren moderner ADAS-Fahrzeuge
Dichtheitsprüfung für sicheres autonomes Fahren
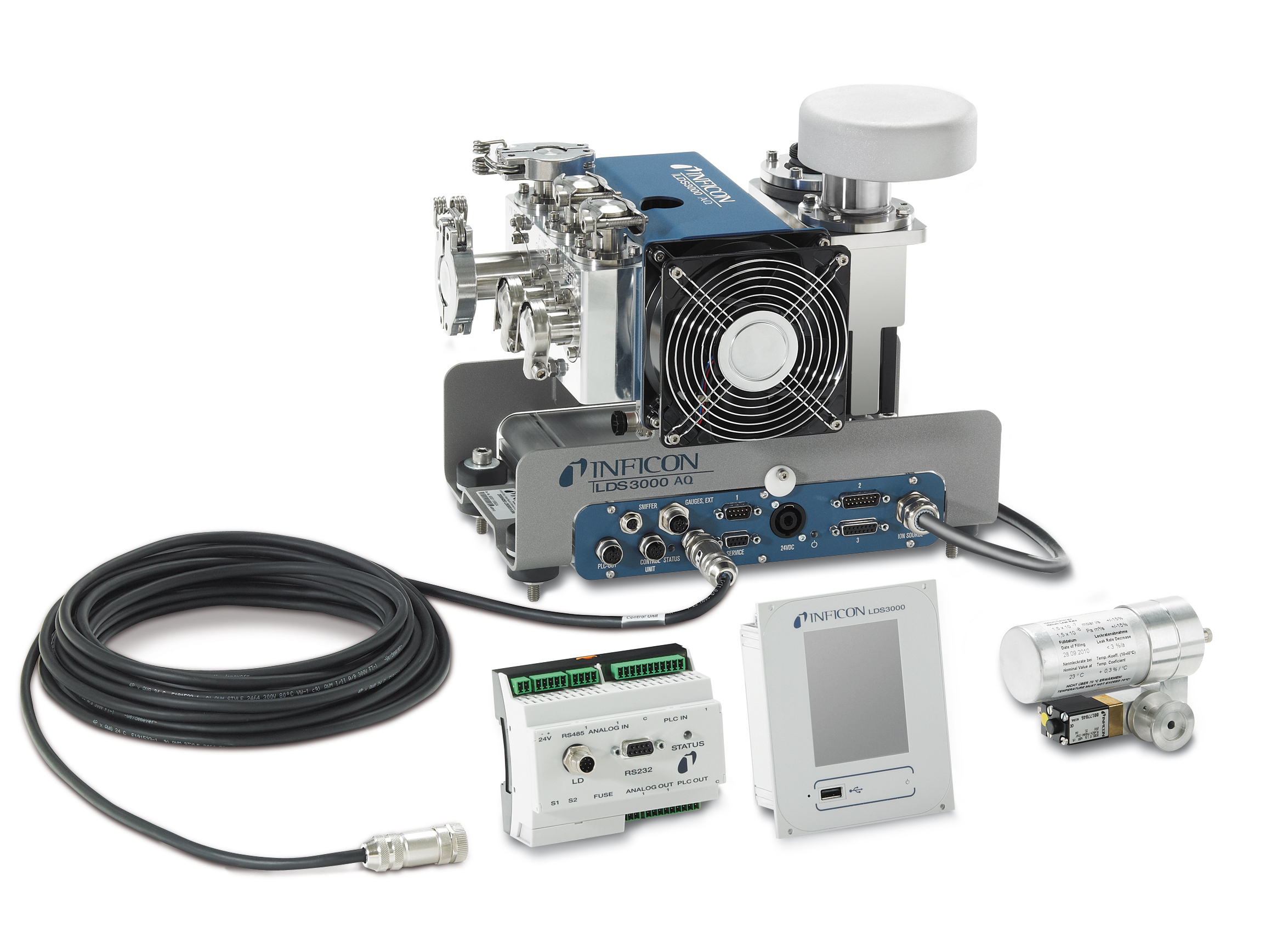
Mit der Weiterentwicklung der ADAS-Systeme und dem Markteintritt von autonomen Fahrzeugen vervielfacht sich die Zahl der verbauten Umgebungssensoren. Während Assisted Driving prinzipiell schon mit einem einzigen Sensor im Fahrzeug beginnt, rechnet man für Pkws, die sich halbautonom fortbewegen, mit rund 16 verschiedenen Sensoren, Kameras und Radarsystemen. Soll sich das Automobil vollständig autonom bewegen können, kalkuliert man mit mindestens 44 Sensoren. Alle diese Elektronikkomponenten und Sensoren im Fertigungsprozess auf ihre Dichtheit zu prüfen, ist unerlässlich, wenn die Elektronik ein Fahrzeugleben von rund 15 Jahren überdauern soll. Besonders streng sind die Anforderungen an ADAS-Komponenten für die drei höchsten Autonomieniveaus: Bedingungsautomatisierung (Level 3), Hochautomatisierung (Level 4) und Vollautomatisierung (Level 5).
Fahrzeugelektronik muss üblicherweise in einem Temperaturbereich von -40 bis 150 °C funktionieren. Betrachtet man die ADAS-Sensortechnologie sind die Anforderungen im Zweifelsfall weit höher. Ein Six-Sigma-Ansatz, der 3,4 Fehler unter einer Million Fällen gestattet, wäre in diesem Kontext unvorstellbar. Hersteller von ADAS-Komponenten verfolgen vielmehr eine Null-Fehler-Strategie mit weniger als einem Versagensfall unter einer Milliarde Teilen. Alles andere wäre für Fahrzeuge, die sich im dichten Stadtverkehr ebenso wie bei Autobahngeschwindigkeiten autonom oder teilautonom bewegen sollen, aus Sicherheitsgründen nicht tolerierbar.
Das Gehäusematerial als Dichtheitsfaktor
Der zentrale Feind aller elektrischen und elektronischen Komponenten in einem Fahrzeug ist das Wasser, schon weil naturgemäß die Gefahr eines Kurzschlusses besteht. Entsprechend wichtig ist die Wasserdichtheit der Gehäuse elektronischer Komponenten. Dies bedeutet, dass diese Gehäuse in der Regel den Schutzklassen IP67 oder sogar IP69K genügen müssen. Dabei besteht zwischen dem Gehäusematerial und den Grenzleckraten, gegen die auf Dichtheit geprüft werden sollte, ein enger Zusammenhang. Dabei ergeben sich bei Gehäusen aus Kunststoffen oder auch aus Stahl weniger strenge Anforderungen als bei Gehäusen aus Aluminium.
Denn wie leicht Wasser durch einen Leckkanal mit definierter Länge und Durchmesser in ein Gehäuse eindringt, hat entscheidend damit zu tun, wie leicht sich ein Wassertropfen vom Gehäusematerial ablösen kann. Aluminium beispielsweise ist viel kritischer als Kunststoffmaterial, weil sich Wasser von Aluminium viel leichter ablöst. Um die Wasserdichtheit von Kunststoffgehäusen sicherzustellen, lassen sie sich mit der einfachen Akkumulationsmethode gegen eine Helium-Leckrate von 10-3 mbar∙l/s prüfen. Das Gehäuse wird dafür mit dem Prüfgas befüllt. Dann misst man, wie viel Prüfgas aus einem etwaigen Leck in einem bestimmten Zeitraum aus dem Gehäuse in eine simpel aufgebaute Akkumulationskammer austritt. So errechnet sich der Volumenstrom des austretenden Prüfgases und damit die konkrete Leckrate.
Vakuumprüfungen für Aluminiumgehäuse
Werden Gehäuse nicht aus Kunstoffen oder Stahl, sondern aus Aluminium gefertigt, sind Prüfungen gegen tausendfach kleinere Lecks erforderlich. Für solche Tests gegen Grenzleckraten von 10-6 mbar∙l/s kommt praktisch nur die Heliumprüfung in der Vakuumkammer infrage. Das Aluminiumgehäuse wird dazu mit Helium befüllt und in eine Kammer gebracht, aus der man die Luft evakuiert. Damit sind auch kleinste Mengen Helium nachweisbar, die in das Vakuum der hochdichten Kammer austreten. Besteht allerdings keine Befüllmöglichkeit am Gehäuse – etwa weil es bereits hermetisch abgedichtet ist – verwendet man die sogenannte Bombing-Methode. Beim Bombing wird das Prüfteil zunächst einer Helium-Atmosphäre ausgesetzt, sodass das Prüfgas durch etwaige Lecks ins Gehäuseinnere eindringen kann. Erst dann kommt dieses Prüfteil in die Vakuumkammer, in der das Helium durch die Leckstelle wieder austritt.
Steuermodule mit Gore-Tex-Membran
In manchen Fertigungsprozessen wird die Notwendigkeit der späteren Dichtheitsprüfung bereits berücksichtigt – und das Bombing vermieden. Dafür befüllt man das Gehäuse unmittelbar vor seiner endgültigen Abdichtung mit einem Prozent Helium. Um gegebenenfalls austretendes Helium bei der späteren Prüfung nachzuweisen, ist dann aufgrund der geringen Prüfgaskonzentration oft wieder die Vakuumkammer erforderlich. Es gibt allerdings noch einen anderen Weg, das Prüfgas ins Innere zu bringen. Steuermodule sind sehr oft mit einer semipermeablen Gore-Tex-Membran ausgestattet, die temperaturbedingte Luftdruckunterschiede ausgleichen und einen Druckdifferenz zwischen dem Gehäuseinnern und der Umgebung vermeiden soll. Die Tatsache, dass solche Gehäuse durch ihre Membran gleichsam atmen, macht man sich zunutze, um sie bei der Dichtheitsprüfung mit Helium zu beaufschlagen. In einer Akkumulationskammer oder in einer Vakuumkammer ist das austretende Prüfgas dann nachweisbar. Allerdings hat die Prüfung in der aufwendigen Vakuumkammer gegenüber jener in der einfachen Akkumulationskammer immer den Vorzug einer höheren Geschwindigkeit und kürzerer Taktzeiten. Denn bei der Vakuumprüfung ist es unnötig, darauf zu warten, bis sich genügend Prüfgas in der Kammer angesammelt – oder akkumuliert – hat.
ADAS-Sensoren müssen gasdicht sein
Bei vielen ADAS-Sensoren ist es wichtig, dass sie nicht nur wasser-, sondern auch gasdicht sind. Eine Komponente, die nicht gasdicht ist, birgt immer die Gefahr, dass eingedrungene Luftfeuchtigkeit bei Temperaturänderungen kondensiert und ihre absolute und dauerhafte Funktionssicherheit beeinträchtigt. Ein Beschlagen durch Luftfeuchtigkeit ist für LIDAR (Light Detection And Ranging)- und RADAR-Sensoren (Radio Detection And Ranging) ähnlich problematisch wie etwa für eine Kamera-Optik. LIDAR-Sensoren dienen der Erfassung von Objekten in mittleren Distanzbereichen. Dagegen decken RADAR-Sensoren einerseits den Nahbereich um das Fahrzeug ab und scannen andererseits Hindernisse auf größere Distanz. Hinzu kommen noch Ultraschall-Sensoren für Einparkvorgänge. Um die Gasdichtheit der sicherheitskritischen LIDAR- und RADAR- Komponenten zu verifizieren und jedes Eindringen von Luftfeuchtigkeit auszuschließen, sind Dichtheitsprüfungen gegen sehr kleine Grenzleckraten im Bereich von 10-6 bis 10-7 mbar∙l/s nötig. Dies macht eine Helium-Vakuumprüfung notwendig. Auch für die Gasdichtungen in einem Sensorgehäuse, durch die strom- bzw. signalführende Kabel ins Innere geführt werden, gelten dieselben strengen Dichtheitsanforderungen. Bei US-amerikanischen Herstellern von LIDAR- und RADAR-Sensoren beispielsweise ist darum die Heliumprüfung in der Vakuumkammer bereits die Methode der Wahl.
Druckverfahren vs. Prüfgasmethode
Weltweit werden derzeit noch viele Sensoren mit dem unempfindlicheren Druckabfallverfahren geprüft. Auch die tendenzielle Unzuverlässigkeit ist ein Problem der Druckabfallprüfung. Denn wenn sich die Temperatur während der Druckabfallprüfung nur minimal erhöht, steigt entsprechend auch der Druck, was potenzielle Lecks verschleiert. Fällt die Temperatur dagegen ab, sinkt auch der Druck, und es kommt zu fälschlich identifizierten Lecks und Fehlalarmen. Gerade im Fall von ADAS-Komponenten und -Sensoren spricht aber nicht nur die weit höhere Empfindlichkeit dafür, anstelle herkömmlicher Druckverfahren Prüfgase einzusetzen – es ist ihre Zuverlässigkeit und Reproduzierbarkeit, die Prüfgasmethoden unersetzlich macht.
Das Ziel der Hersteller von ADAS-Komponenten, eine Fehlerrate von unter einem Fall auf eine Milliarde Teile zu erreichen, erscheint ehrgeizig, ist aber unverzichtbar. Die Funktionsfähigkeit aller sicherheitskritischen Systeme muss langfristig gewährleistet sein. Und die Sensoren – sozusagen die Sinnesorgane autonomer Fahrzeuge – sind definitiv sicherheitsrelevant. Diese Komponenten bei der Fertigung sorgfältig auf ihre Gasdichtheit zu prüfen und kleine Lecks auszuschließen, reduziert die Gefahr eines Eindringens von Luftfeuchtigkeit. Sensoren, die mitten im Betrieb gleichsam erblinden, wären auf den höheren ADAS-Autonomiestufen unvorstellbar.
Autorin
Sandra Seitz, Market Manager Automotive Leak Detection Tools, Inficon
Kurz erklärt: Vakuummethode
Die integrale Dichtheitsprüfung in einer Vakuumkammer ist häufig ein Inside-out-Test. Der Prüfling wird zunächst in einer Kammer platziert, entweder manuell durch einen Operator oder automatisch mit einem Roboterarm. Eine Pumpe erzeugt ein Vakuum in der Prüfkammer und das Innere des Prüflings wird über entsprechende Anschlüsse mit Helium befüllt. Zwar ist diese Methode aufgrund der strengeren Leckratenanforderungen für die Kammer und durch die kostspielige Vakuumpumpe relativ teuer, trotzdem bietet sie einige entscheidende Vorteile: Erstens ist die Heliumprüfung in der Vakuumkammer die empfindlichste aller Prüfgasmethoden. Das für die Erkennung von Helium verwendete Massenspektrometer kann unter Idealbedingungen Leckraten bis zu 1x10-12 mbar l/s erkennen. Die Vakuummethode ist gut für die Prüfung auf Fertigungslinien und für viele automatisierte Produktionsprozesse geeignet, bei denen jedes Teil einer integralen Dichtheitsprüfung unterzogen wird. Ein weiterer Vorteil der Vakuummethode sind die kurzen Zyklen und die schnellen Zykluszeiten, insbesondere bei vollautomatisierten Prüfsequenzen. Darüber hinaus ermöglicht die Empfindlichkeit der Vakuummethode oftmals eine deutliche Reduzierung der Helium-Konzentration, auf nur rund ein Prozent, wodurch auch die Kosten für das Prüfgas sinken.
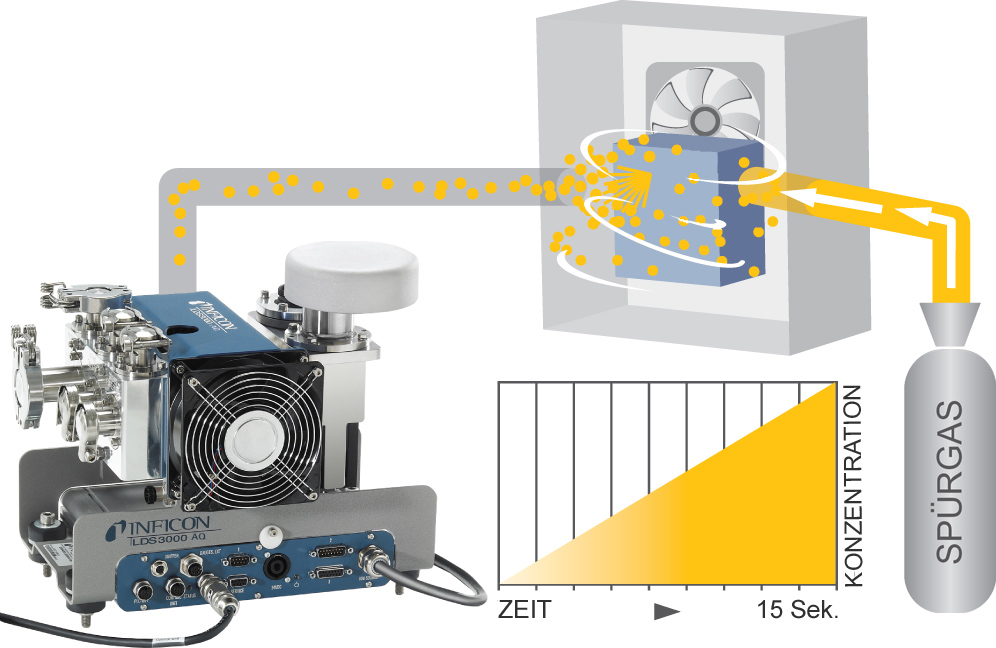
Kontakt
Inficon GmbH
Bonner Str. 498
50968 Köln
+49 221 56788 0
+49 221 56788 90